
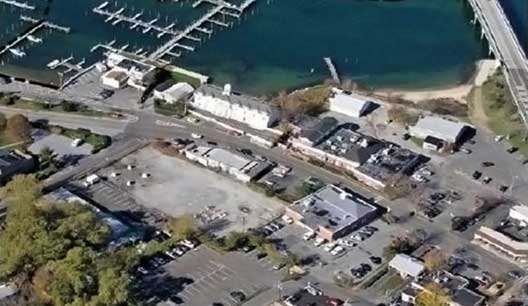
The Sag Harbor former Manufactured Gas Plant Site is an approximately 1 acre property located in the Village on the east side of Bridge Street at its intersection with West Water Street and Long Island Avenue.
The property was purchased by Captain David Cogden in 1859 and it is said to have been used to manufacture gas from coal or rosin. Gas was manufactured by a succession of companies on the site and distributed in the Village and to nearby communities until 1931. The Long Island Gas Corporation took control and increased production capacity in 1916, and in 1929 LILCO purchased the site. After acquisition, LILCO linked the company’s gas distribution system in eastern Long Island to Bay Shore. With the shift to serving as a distribution link in 1929, gas storage capacity was increased significantly, including aboveground high-pressure storage tanks, and production at the Sag Harbor site ceased. The facilities for gas manufacture were later dismantled and removed from the site. The facilities for gas storage (the Hortonsphere) were decommissioned and dismantled in 2006. At the height of its use, the site included four gas storage tanks, three purifying houses, several oil tanks, a tar separator and several other production buildings.
In 1998, the site was added to the State's Registry of Inactive Hazardous Waste Disposal Sites (Registry), as a class 2 site. A class 2 site "poses a significant threat to the public health or environment and requires remedial action." As a result of this classification, KeySpan (now National Grid) entered into an Order on Consent with the NYSDEC in 1999 to perform a remedial investigation/feasibility study and remediation of the site.
The Remedial Investigation was conducted between 1999 and 2002, followed by Supplemental Investigations. The investigation included soil borings to determine the nature and extent of contamination in the subsurface soils, as well as the installation of monitoring wells and the placement of temporary groundwater probes to determine the extent of the groundwater contamination. Soil vapor sampling as well as indoor air sampling in nearby commercial buildings were also part of the investigation.
The investigation confirmed the presence of contaminants typically associated with an MGP operation. These contaminants include BTEX compounds and polycyclic aromatic hydrocarbons (PAH’s). BTEX compounds are benzene, toluene, ethylbenzene, and xylene. These are volatile hydrocarbons found in most petroleum products such as gasoline. They are less dense than water and will form sheens on top of water. PAHs are made up of several semi-volatile compounds, also found in many petroleum products, such as asphalt. These compounds tend to be denser than water and are not readily dissolved or broken down in the environment.
BTEX and PAHs are most often found in a mixture known as coal tar (also known as a dense non-aqueous phase liquid, or DNAPL due to its capability to sink in water and the fact that it does not easily mix with water). It is a dark, viscous fluid with a distinctive acrid odor. Coal tar was the mixture of the residual substances which condensed out of the manufactured gas before it was piped to individual customers.
The coal tar and its chemical constituents on the Sag Harbor site were mostly found immediately underneath the locations of the old gas holders and tar separation tank. From there the coal tar (DNAPL) followed a layer of peat, silt, and clay which underlies the site and migrated away from the site, mainly to the south. The tar and its constituents were also the source of the groundwater contamination which traveled north and northwest off the site, towards Sag Harbor Cove. This contamination is made primarily of BTEX compounds, although some PAHs are found in the plume fairly close to the site.
Based on the information gathered during the investigation it was determined that there were no current pathways through which the community could be exposed to the contaminants on the site or in the groundwater plume. Indoor air monitoring in commercial as well as residential buildings showed that all of the potentially harmful substances associated with former MGP operations were either not present in indoor air or at levels below the background levels which are derived from the routine finding of these substances (which have many sources in addition to former MGP operations) in normal air. There were also no data to suggest that the contaminants are having an adverse impact on fish or the transient wildlife in the community.
Based on the results of the investigation and after an analysis of remediation alternatives, the New York State Department of Environmental Conservation, after a Public Meeting and taking of public comments, approved, in a Record of Decision announced in 2006, a Remedial Action Plan for the site. The key elements of the Remedial Action Plan were the excavation of MGP tar contaminated soils to roughly ten feet below ground surface, installation of passive tar collection wells, installation of a sub-surface barrier wall, covering areas of the site with clean fill, development of a site management plan, periodic assessment of the effectiveness of the remedy, and, if necessary, installation of vapor mitigation structures under existing or new structures on or near the site.
National Grid has now completed the Remedial Construction, under a Remedial Design plan approved by the New York State Department of Environmental Conservation and the New York State Department of Health. The agencies provided oversight during the construction.
The site is now in the Operations, Maintenance and Monitoring phase with periodic groundwater sampling.